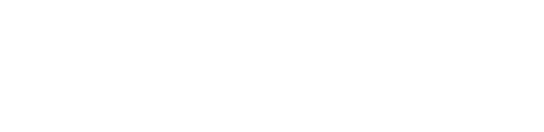
The business case: reduce cost and bring down the carbon footprint
Like many healthcare facilities, Cooley Dickinson of Northampton, Massachusetts was looking for ways to reduce energy costs as well as their carbon footprint. Cooley Dickinson has a unique energy system that is powered primarily from a biomass boiler. This low-cost fuel not only saves money, but also allows the hospital to meet its thermal energy need with a renewable fuel. Cooley Dickinson also uses steam to generate cooling water in warmer months with absorption chillers. The implementation of Microsteam® Turbines allowed the facility to generate high-value renewable power with little change to the downstream infrastructure.
The installation
Cooley Dickenson installed two (2) Microsteam® Turbines in 2010 at distinct and separate steam applications. While most multi turbine installations run turbines in parallel at the same pressure drop, the hospital’s use of absorption chillers created an additional opportunity to generate power in summer months. The primary 300 MAWP biomass boiler generates steam consistently at 275 psig, and steps down to 75 psig by Turbine A, in parallel to a pressure reducing valve, for distribution to hospital campus buildings. In warmer months, Turbine B is deployed by further stepping down steam from 75 psig to 14 psig for the chilling units. This elegant turbine-in-series configuration allowed Cooley Dickinson to maximize power output from their existing steam system.
Key Numbers
Primary Boiler MAWP
Primary Boiler Fuel
Year Installed
Inlet Pressure
Outlet Pressure
Flow
Generation Capacity
Annual Generation
Energy Savings
GHG Reductions
Project Pay Back
Microsteam® Turbine A
300 psig
Biomass
2010
275 psig
75 psig
18,000 lbs/hr
275 kW
1,800,000 kWh/yr
$216,000/yr
940 Tons/yr
2 yrs
Microsteam® Turbine B
300 psig
Biomass
2010
75 psig
14 psig
13,000 lbs/hr
190 kW
1,050,000 kWh/yr
$132,000/yr
475 Tons/yr
3 yrs
The long-term benefits
The Microsteam® Turbines have been operating for over 12 years since commissioning, saving Cooley Dickenson millions of dollars in electrical power costs, and reduced over 15,000 tons of CO2. Beyond these significant benefits, one key project driver for Cooley Dickenson to implement these turbines was their space-efficient footprint. Microsteam® Turbines are vertically configured to minimize necessary floor space as well as negate the need for expensive civil and mechanical modifications to the facility. Hospital pressure reduction stations rarely have available floor space for larger conventional, less-efficient back pressure turbines, which has made these types of installations to existing facilities so rare.
Another primary long-term benefit of this installation is the ease of operation. With modern PLC controls and utility grade safety features, the turbines have allowed staff to quickly learn how to operate, maintain, and not fall back on the ease of simple PRVs that waste valuable power generation opportunities. Like many hospital facilities, Cooley Dickinson’s plant staff has changed over time, and despite not being present upon procurement, design, and start-up, the current staff continues to rely on and appreciate the benefits of the Microsteam® Turbines a dozen years later.
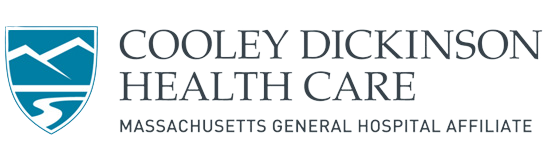
“These are cool little machines that just work.”
Matt Couture, Energy Plant Manager
Certified. Trusted. Proven
Discover the untapped energy in your steamsystem. Request an assessment from our expert engineers at thermal@nlineenergy.com
Do you have steam? Would you like to make clean, renewable power? Give us a call! Our experts can instantly assess your opportunity.
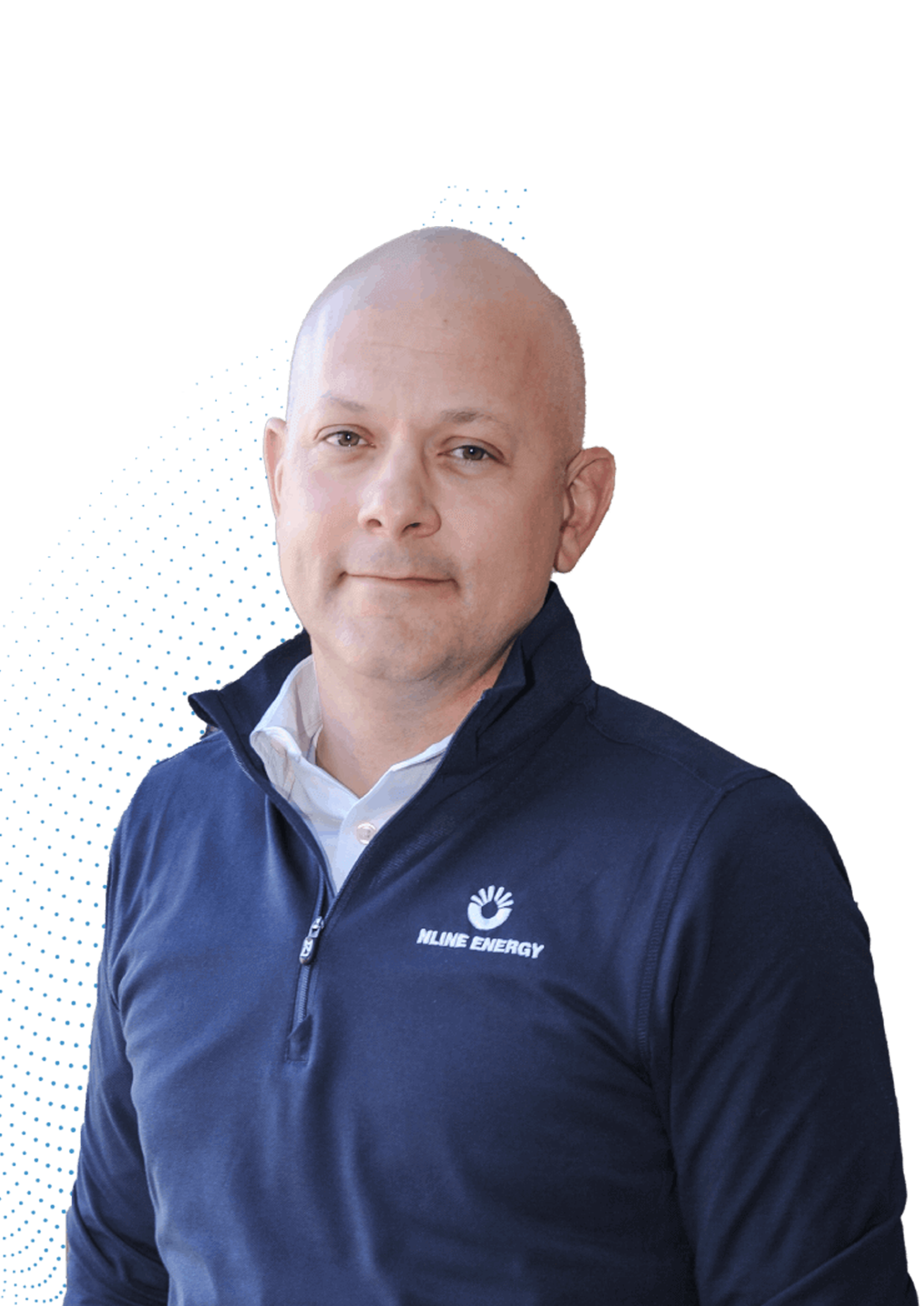
Nate Turner, Chief Commercial Officer
Do you have steam? Would you like to make clean, renewable power? Give us a call! Our experts can instantly assess your opportunity.